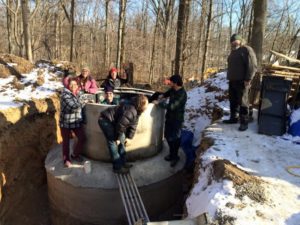
“Gassy girl” is America’s first 10m3 Puxin biogas system. She was built by the Solar CITIES US team just before Christmas of 2014!
January 2, 2015
Let freedom ring! In the land of the Liberty Bell, a new bid for independence has been launched with the creation of America’s first Puxin 10m3 biogas system at the homestead farm of Jody and Bob Spangler. Built by our Solar CITIES team with help from Envisaj Mercy students and community members, the successful completion of a biogas system of this size in the winter gives us a chance to evaluate performace throughout the cold months. It also allows us to make the necessary improvements so that this size class of small-scale biogas can get off the launchpad in the US.
The most exciting thing about the end of 2014 for those in our movement is that we can truly say that America’s first Puxin family-size biogas food waste digester was built of the people, by the people for the people! And some said it couldn’t be done. And some felt it shouldn’t be done. But we knew it had to be done! Go team Solar CITIES/Envisaj! Truly happy New Year!
Costs
What have we learned from this precedent-setting experiment in the northeast?
Our 10-cubic meter Solar CITIES Puxin biodigester, the first of its kind in North America, is turning out to cost less than we thought in materials, coming in at about $100 per cubic meter. We will see what insulation costs, but this is a good harbinger for the future if in our movement like minded individuals provide labor and tools in kind, as we’ve proposed!
We used 41 bags of Portland cement weighing 42 kg each costing $10.47 each for a total cement cost of $429.27.
We used 55 bags of All purpose cement weighing 18 kg and then we brought in 43 more bags weighing 22.6 kg.
The heavier bags were $6.99 each and the lighter ones were $3.15 each. We spent $474 on sand. We didn’t buy gravel as it was given to us, but we will calculate the amount and cost.
We used 1 part cement, 2 parts sand and 2 parts gravel. We used 13 steel mesh rectangles (42 inches x 84 inches), costing $7.25 each (instead of rebar; no need to bend and tie). We also used 16 rebars 1/2 inch by 12 inch, costing $1.10 each, which we used as pegs in a circle between the inner and outer molds anchored in the floor slab to tie the mesh to (which goes between the inner and outer molds and on the shoulders and around the neck).
Thus our costs were $1075 in basic materials. ($1014.94 for materials and $60.90 for tax).
When we built this design in Brazil, digging was one of our big line items. At the Spangler farm, we didn’t have to rent a backloader because they own a construction company and had their own.
We have decided in the future, however, to build above ground and are hoping to do our next build as a 4m3 Puxin (using the same molds, but only the bottom portion) inside the small greenhouse at Mud Creek Farm with Christopher Lindstrom. Since the greenhouse already has a concrete floor, we will save on the slab costs, which are actually a substantial part of the build effort and cost. Building in a greenhouse means we can build in the winter. The Puxin will act as a thermal mass to keep the greenhouse temperature warm and regulated. The displaced horizontal surface of the floor of the greenhouse will become an elevated growing area; plants will grow on top of the digester and on the shoulders, so we lose no greenhouse space. The sides will enable trellising and vertical farming so in fact, putting a Puxin in a greenhouse above ground INCREASES the growing area of the greenhouse even while it regulates temperature. By burning the gas in a generator in the greenhouse, we will get heat, power, and CO2 for the plants. My thinking is that we should try to build above ground in greenhouses as often as possible.
Our model is to build in communities that donate in-kind labor and tools. We aren’t in business, so we don’t have a bottom line to worry about. Our role is to introduce the technology and get systems going that will give people the “wow” moment and make them love biogas. Then these communities can decide which systems to go for. I am personally recommending professionally-produced home biogas systems that are factory made and guaranteed, such as Tevagas, Hestia, Flexi, and other commercial products wherever available. We teach people to build IBCs and ARTIs if they want to go the DIY route. We will be doing installations of Puxin’s in the US and Europe in community locations as showcases. But we are not recommending this as a business model. Labor is always a crucial factor that makes those equations change. Our is an educational effort.
Materials
Our colleagues at the Tamera Solar Village in Portugal, where we are building Europe’s first Solar CITIES Puxin, calucated that if all walls are 10cm, then the amount of concrete needed would be: basement 1m³; stomach wall 1.3m³; cover of the stomach: 0.8m³; neck wall; 0.6m³; at all 3.4m³:
Jody Spangler just did the calculations for our first build in the US for a 10m3:
PAD: 11 x 11 feet x .33 feet deep (that equals a 4 inch thickness of the slab) = 39.93 cubic feet divided by 27 to equal cubic yards. We thus used 1.47 cubic yards, which we order from the truck as 1.5 cubic yards. In cubic meters that would be 1.14 cubic meters of concrete for slab.
WALLS: 34.5 feet x 4.7 feet x .33 feet (10 cm) thick = 53.5 cubic feet/27 = 2 cubic yards, or 1.52 cubic meters of concrete for walls (for 10 cubic meter wall, full size mold, NOT including the shoulders)
SHOULDERS: (approximation by concrete bags since not uniform geometry): 1.33 cubic yards = 1.01 cubic meters.
NECK: 19.2 feet by 3.7 feet by 0.33 feet thick = 23.5 cubic feet/27 = .86 cubic yards = 0.65 cubic meters.
Neck is less than a cubic yard of concrete (about 7/8), so on the day of that pour you are safe with a cubic yard and you’ll have concrete left over to put hand prints in.
Our calculations based on what we actually USED is very close to what Solar CITIES Europe have calculated for what they intend to use. We used a bit more concrete for the shoulders but that is because we made them extra thick. We didn’t need to. In total we used 5.69 cubic yards of concrete which is 4.35 cubic meters, comparing to their theoretical calculation of 3.4 cubic meters — the differences being in our over thick shoulder and our slab (pad) which was thicker and maybe wider.
For those doing a 4 cubic meter digester using the Solar CITIES Puxin molds:
You use 40% of the amount of concrete used in a 10m3 builds WALLS (the rest stays the same).
For a 6 m3 digester (also permitted by our molds) you would use 60% of the concrete used for the walls. Simple right?
Now since you are shortening the wall heights and volume of digester you can make a thinner slab, reducing from 4 inches to 3 inch base thickness.
For the 6m3: Walls = 1.2 cubic yards or 0.91 cubic meters
Pad reduced to 3″ for less weight and water volume so need only 30.25 cu feet or 1.21 cubic yards = 0.91 cubic meter (use 4 inch slab for 10m3! 1.14 cubic meters).
For the 4m3: Walls = 0.8 cubic yards = 0.61 cubic meter.
Neck and shoulder: the song remains the same (unless you are building a Led Zeppelin!).
We used 42.5 kg bags of Portland cement mixed with sand and gravel at a ratio of 1:2:2.
We used for shoulders: 7 bags Portland.
For neck we used: 5 bags Portland
In the slab pad we used: 10 bags cement (with 1.5 tons of sand and 1.5 tons of 2A modified stone gravel)
For walls (10m3) we used 20 bags of cement.
We have two left for cover slab, but we have decided NOT to make a cement cover since we aren’t walking or driving on top of digester and want to be able to lift cover, like the plastic ones they used in Shenzhen that are in the videos I posted here:
Instead of plastic lids, however, we will use Plastic board like Trex, with spray foam on it for seal and insulation.
In the end, we used 40 bags of 42.5 kg Portland cement for the 10m3. That equals 1700 kg. Puxin estimates an average of 1400 kg. Our overage of 300 kg is accounted for by the thicker wider slab we made. Be careful, you can waste a lot of concrete in the slab. Puxin estimates a round hole slab and we made a square slab so all the edges took up concrete! In the future we will get this down to around 1400 kg, but you are safe, based on our build here, if you have 1700 kg of concrete on hand.
The Puxin manual says:
The construction material needed to install the 10 m3 digester:
Material
Q’TY
Smashed stone
4.0 M3
Sand
3.5 M3
Cement
1400 Kgs
Brick
100 Pcs
Plastic pipe
4 Meter
It thus seems that unlike us, they are using a 1:1:1 ratio of cement to sand to stone.
Our experience is that there is variance around the world in the mix of concrete used. Your safest bet is to work with what the locals use and know.